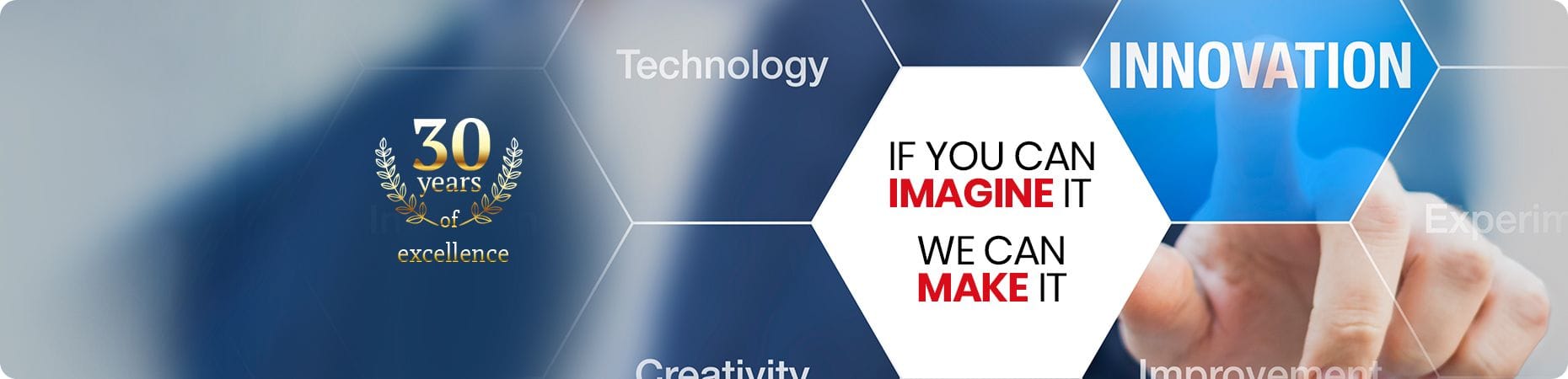
Vacuum Forming Gold Coast
P&M Plastics have several specialised Vacuum Forming machines that have a variety of applications, utilising different plate sizes that are driven by advanced CNC software to accurately adjust the individual heaters, the time, vacuum pressure & ensure that the formed part is consistent every time.
P&M Plastics currently has five vacuum forming machines currently in use:
- Waeco Vacuum Forming machine Single heat platen Manual controlled - capacity 1380 x 760
- Leading edge Vacuum Forming machine Single heat platen CNC controlled - capacity 1500 x 1500
- Leading Edge Vacuum Forming machine Twin heat platen CNC controlled - capacity 2650 x 1830
- P&M Vacuum Forming machine Single heat platen CNC controlled - capacity 3100 x 2000
- Maac Vacuum Forming machine Twin heat platen CNC controlled - capacity 2250 x 1250
Some of the materials typically used in Vacuum forming are:
- Acrylic
- High Impact Stryrene
- High Impact Acrylic
- Polyethylene
- ABS
- ASA
Vacuum forming is performed by heating a thermoplastic material till it reaches a pre-set melt flow index at which point the material can be formed over a Tool / Mould using Vacuum.
All 2D vacuumed plastic components are made from a tool. During the proto-type stages the tool is made from wood or MDF and made in house on our 3D routers or made in our Tooling Dept.After trials have been run, adjustments made and samples approved the tool is then manufactured from either fibreglass or a Aluminium Epoxy material.
Once the sheet is Vacuumed formed Jigs & Fixtures cut the components from the moulded sheet.
This operation is performed for low volume components.
P & M Plastics also have the capacity of our CNC Robot Trimmer to trim components from the moulded sheet
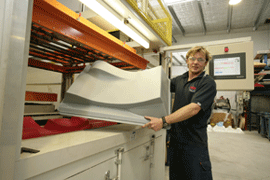
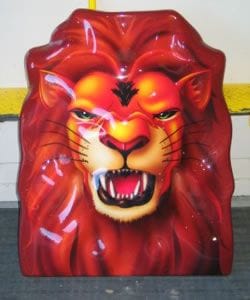
